火力発電用ガスタービン部品はいずれも多品種少量生産であり、当社の強みは、高い技術力と効率的な生産体制を整え、大手企業が手掛けないような手間がかかる加工を積極的に行っていることです。
当社は、もともと製缶・溶接が主体の企業です。それに加えて、非量産の金型プレス加工も行うことにより事業を拡大してきました。
また、ある一社に従属するのでなく、複数の取引先から仕事を受注するようにリスク分散にも努めています。
「ものづくり企業の社長ならば大概は、自社製品を生み出すと
いう夢を持っていると思う。現に、自分は(夢を)持っていたし、
行ってもみた。それは、出入口等の段差に掛けて車椅子等の出入
りを楽にするマグネシウム製携帯スロープの開発でしたが、3年
間で18台しか売れなかったな」と、小峰社長は笑って話してく
れます。
小規模企業にとっては、販売部門まで整え、販売ルートを開拓
することは大変なことです。当社のように、仕事の合間の対応で
の販路開拓は難しいということを痛感したそうです。
しかし、その失敗が、新しいものを作るだけでなく、作り方の
面で進化出来ることを知り、いい経験になったとおっしゃってい
ます。
そのようなお話を聞くと大変苦労をなさったのではないかと思
いますが、「仕事は楽しいし、仕事場にいるのが好きなので、社
長としての苦労は今まで感じたことはない」とのことです。
当社は、産学共同による新技術の開発にも挑戦し続けています。
茨城大学大学院西野研究室と共同で、これまでに耐熱超合金(難加工材)の高精度プレス加工技術を開発しています。
同技術は、経済産業省・中小企業庁「平成21年度ものづくり中小企業製品開発等支援補助金(試作開発等支援事業)」で採択され、H22/1月、深絞り用NC制御油圧プレスを導入、また、H22/7月には、三次元5軸レーザー加工機を導入し、作業の効率化を見出しています。
右図のとおり、L字形リングの製作においては、従来の方法では丸平板の材料を切断・プレス・機械加工していましたが、新たに開発した高精度プレス加工方法では細長形の材料を用い、溶接・プレス加工する事で材料費の約70%低減に成功しています。
材料として使用している耐熱超合金鋼等の金属材料は、取引先からの支給品ですが、価格的に高いものなので、材料費を削減することにより、取引先の原価低減にもつながっています。
また、U字形シールの加工においては、従来方法では7つの工程を経ていましたが、高精度プレス加工方法では4つの工程となり、プレス工程数の削減と、三次元レーザー加工による金型製作費用の圧縮を実現しています。
当社の得意とする技術は、従来より培ってきた耐熱超合金(難加工材)を素材とする精密製缶・溶接技術に、新しく技術開発した高精度プレス金型の設計製作・加工の技術が加わり、製品の幅が広がりました。
事業拡大、新製品開発と夢は大きくなりがちですが、小峰社長の経験から新しいものを作るのはとても難しいとのことです。このため今は、新商品を開発していくのではなく、それよりは、今まで培ってきた当社の技術をもっと伸ばすことに力を入れて、顧客ニーズに徹底的に応え、他社との差別化を図る方向で歩んで行こうとしています。
これからのものづくりのために(新たな取り組み)
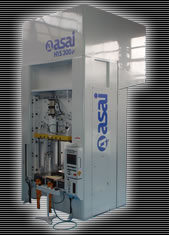
「当社の従業員は28名です。当社の課題は、若い人を育てなければならないということです。年配者には、職人気質の人が多く、立派な技術は持っているものの、その技術を自らが教えていくということが苦手です。自社での勉強会等も行っているが、なかなか成果を上げるのが難しい状態にあります。しかし、最終的には、熟練技術者のそばで技術を見ることによって、習得することも非常に勉強になっています。」
「また、フライス・旋盤加工は、NC機械操作が主体であることから、今の若い人にとっては、パソコンやゲーム感覚で対応できるものとなっています。そこで、従業員には日立地区産業支援センターや県立産業技術専門学院等に通いながら、その中で技術を習得してもらっています。足りない分については、外部からの研修を大いに取り入れてます。更に、当社は、産学官連携にも力を入れており、茨城大学や茨城高専等と技術交流を行い、新しい開発技術を創り出しています。」

「また、当社では、鉄鋼製品からニッケル、コバルト製品とさまざまな素材のものを扱っており、作業工程も部品加工、製缶・溶接加工、機械加工とあり、作業効率と品質を高めるため、数人単位の組を作っての分業制をとっています。組の中で、報告、連絡、相談という流れを作り、作業効率を向上させています。一つのものを作るため、また、その改善にはどうすればよいのかということについて、社員一人ひとりの意識を高めることにもつながっています。組織をしっかりとした形にすることで、確かなものづくりができると確信しています。」
「その証として、品質マネジメントシステムISO9001認証を平成15年に取得し、国際規格に則った対応を心がけています。また、CO2削減、温暖化防止の取り組みとして、平成18年には、環境マネジメントシステムエコステージ1認証も取得し、新たなものづくりを進めています。」
「近年は、若いやる気のある人が入社してきていること(昨年度は4人採用)もあり、社長としても、それに応えていかなければならないという意識を強く持って仕事に臨んでいます。このような姿勢が、現在の当社をささえており、当社の強みの一つです。」と小峰社長は、おっしゃいます。
最後に、小峰社長に「ものづくりとは?」と尋ねたところ、
「製品技術の『安心』『信頼』を生み出すことが基本で、それ
は長年培った技術を裏づけするため、『技をかたちに』心を込
めて一品一品を世に送り出すことである」と答えられました。
当社は、半世紀以上に及ぶ歴史の中で培った熟練の技術とノ
ウハウを生かして、常にコスト面を念頭に効率化を図ることに
力を注ぎ、更に従業員は地元採用と地域に根ざした経営・社会
貢献に努めています。
茨城県北部は、日立製作所という大企業のもとに中小零細企
業が集積し、さまざまなモノづくりを展開している。
新しいものを作るだけがモノづくりではない。新しい技術を
生み出していくこともモノづくりなのだということを知りまし
た。
今後の株式会社小峰製作所のますますのご発展をお祈り申し
上げます。